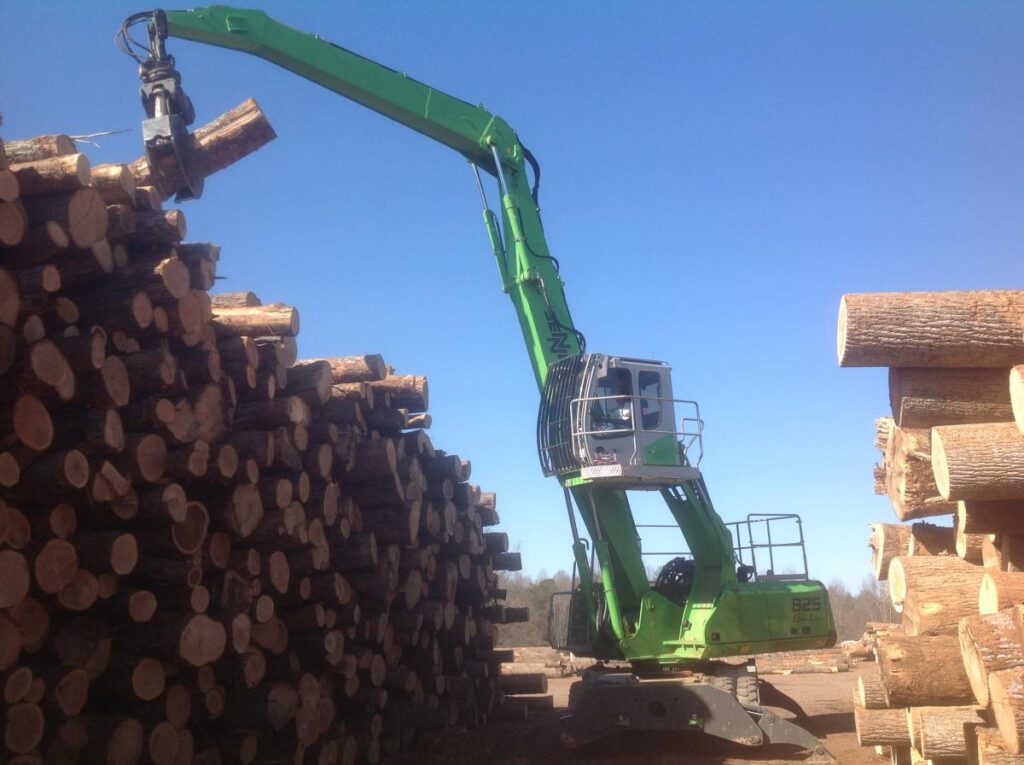
With the 825, Church & Church can now stack logs up to 20+ feet, basically doubling the size of their operation without making the yard bigger!
Wilkesboro, NC – After three generations as a successful hardwood mill, Church & Church Lumber Company was eager for more throughput capacity.
The sawmill in Wilkes County, NC, is now operated by its founder’s grandson, Mark Church. Handling a wide variety of hardwood species, the mill produces primarily poplar, white oak and red oak lumber to be kiln-dried and marketed through another of the family businesses, Select Hardwoods. For years, the facility has consistently output about 23 MMBF per year. But now, Mark Church felt a need for more production.
“Last winter I looked out in the yard and saw all the mud. I saw what was going on out there with the loaders getting stuck and spinning their wheels. I said ‘enough of this’ and we made a huge investment in the yard over the summer to increase our efficiency.”
Making room to grow
Church & Church has been at this location for over 30 years. Mark Church notes that it’s a relatively small space for the volume it produces, just 2.5 acres with another 3/4 acres nearby for overflow. The rebuilt yard includes new roads and new geotextile laid in under 24” of compacted stone to give loading equipment a stable surface to work on.
“But did we make any more room?” Mark asks rhetorically. “Can we inventory the logs we need within this surface area? No… so we asked ourselves, how is this going to increase our throughput?”
Church and his team realized that, to recoup the investment and meet new production goals, there was only one way to increase the yard’s capacity: go higher.
“That’s the trick!”
Up to then, Church & Church was using traditional log-handling equipment, including a knuckleboom loader to sort logs as they arrived by truck, plus wheel loaders to stack them and unload from the ricks. Mark talked to his local equipment dealer, Mark Nelson at ASC Volvo, about upgrading to stack higher. The two discussed getting a wheel loader the next size up, with extra extensions to increase the reach. But in the end, that solution would only give the yard another 2 ft. in stacking height.
Church recalls, “I said, 2 feet…that’s not enough. I want to go higher. That’s when Nelson suggested that we go see SENNEBOGEN’s purpose-built material handlers in action. And I said what in the world is a SENNEBOGEN?”
Church gathered his forester and yard manager to visit the log yard, about 60 miles from their mill. “They handle mainly softer woods with more uniform lengths and diameters than ours. Our wood is harder to stack, but I understood that the principle would be the same.”
“Then, when I saw that cab go up in the air I said Oh yeah – that’s the trick!”
High-stacking hardwoods
The high reach of a SENNEBOGEN log handler would allow Church & Church to stack logs to heights up to 20+ feet – effectively doubling the yard’s inventory capacity. The purpose-built machine features an elevating cab that raises the operator to a perfect eye level. The extra reach and cab elevation answered many of Church’s concerns.
“I like the safety aspect of it,” he says. “I like that you’re actually up over the rick, looking down on the logs, plus being able to place the logs where you want. Stacking accurately is important with the variation you get in the length of the logs and the variation in diameter from the small end to the butt end – especially with that first cut at the stump.”
Church admits that he was still “a bit leary” of how high the SENNEBOGEN could stack, in actual practice. He was concerned for the safety of the loaders, when they came to destack logs from the ricks. Another concern was handling the logs during the summer months, when they dry and the bark tends to fall off the logs in handling. “It makes the logs slippery and harder to handle.”
Protecting yard safety
ASC Volvo arranged to bring a SENNEBOGEN machine from another location for Church & Church to test out. “We could see that the demo machine was larger than what we needed. But it was the right idea.”
To answer his concerns about logs potentially rolling out of the rick onto his loaders, Church planned to have an extra shift unload the ricks at night for the next day. “However, you can unload the ricks safely,” he reports. “Today we have an operator destack in the daytime whenever there’s a break in the yard. As our new yard became so much more efficient, we didn’t have to add the night shift. It’s worked out beautifully. We’re stacking higher and it hasn’t cost me any more for time or another shift.”
“The maneuverability of the SENNEBOGEN 825 works for us. We can move it right up beside a rick and use it to sort the logs, like we did before with the knuckleboom. Its reach is better, its visibility is better and we got a larger grapple to move the logs more efficiently.”
“Overall, I love the machine. If you compare the versatility of this machine versus a wheel loader, there is no contest and the cost is about the same. When I went to SENNEBOGEN’s parts warehouse in Stanley, NC, I was impressed. With all the parts that were there, the booms, the engines in stock, I thought ‘this is a good company.’ I had never heard of SENNEBOGEN, so I wondered about what if there’s a problem. But when I saw that facility, I knew I could take that concern off the table.”