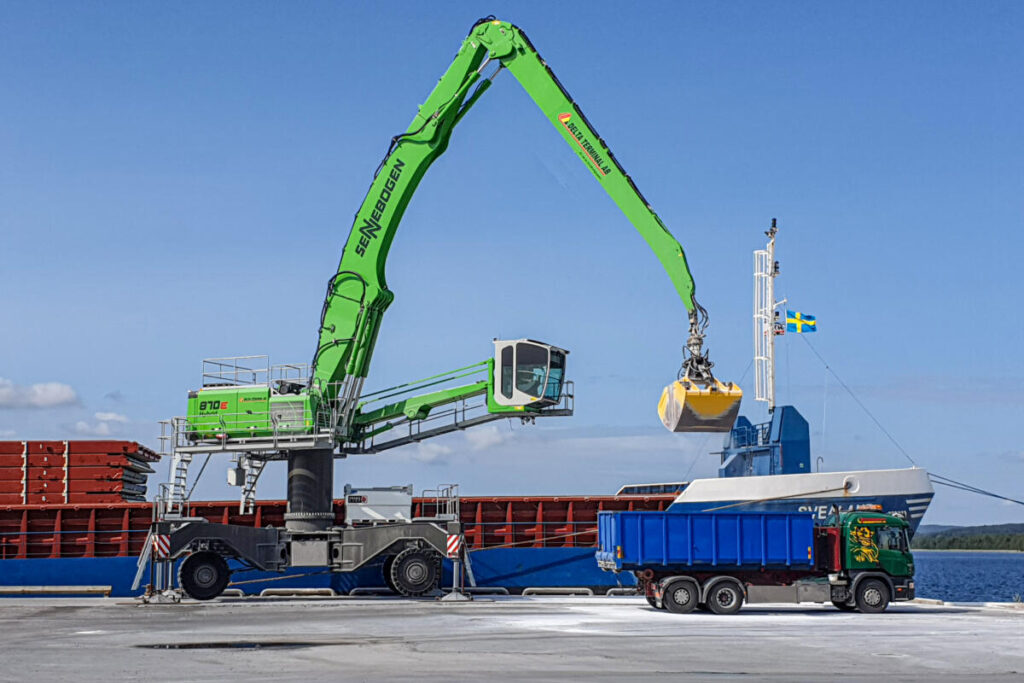
Perfect view of the ship’s hull and the truck’s loading area: Delta Terminals operators work at a viewing height of 36 ft. (11 m) thanks to the liftable, large-capacity Mastercab.
Söråker, Sweden – In 2018, Delta Terminal put a customized SENNEBOGEN material handler into operation in the Port of Söråker, Sweden. Thanks to a rubber-tired undercarriage, its 78 ft. (24 m) reach and excellent visibility for loading and unloading ships, the 870 E material handler proved to be the ideal solution for their operation. Designed for the harsh climatic conditions of the far north, the SENNEBOGEN handles the maritime weather and significant temperature changes with ease in an unparalleled manner. What was Delta Terminal’s final conclusion? When it comes to major investments like this, it pays to dig deep into the smallest details during the planning process and consider the long-term benefits.
More lightweight than the previous solution, more reach, high maneuverability, a particularly robust design and the necessary visibility for ship loading – these were Delta Terminal’s requirements for its 870 E material handler in Söråker, Sweden.
Johan Stenström, Operations Manager at Delta Terminal explains, “Along our 590 ft. (180 m) dock, we handle around 50 ships a year with a hull depth of up to 7 m (23 feet).”
Therefore, the material handler has to be stable on the dock in order to position large loads with pinpoint accuracy, especially inside the ship’s hull. Here, the special mobile undercarriage from SENNEBOGEN entered the picture. Due to its star-shaped undercarriage construction with pivoting outriggers, it creates a particularly large support base of around 680 sq. ft. (63 sq. m). In this way, both the weight of the 120-ton machine and the forces occurring during slewing are transferred to the ground and the ground pressure is evenly distributed. As a mobile version, the large port machine remains extremely maneuverable and can be used throughout the site, whether on the dock or at their storage facilities.
15% More handling capacity in import and export business
Johan Stenström, who manages port logistics at Delta Terminal shares operational details, “Every year, we move around 200,000 tons of material from the ships to the trucks or vice versa. For us, it was very important to be able to have the flexibility of handling a great variety of products in the most efficient way. Above all, we now benefit from the extra reach that the SENNEBOGEN 870 E gives us!”
Industrial waste, general cargo and timber are all part of the Swedish company’s daily business. However, bulk materials such as salt, magnesium or quicklime make up about 60% of the material to be processed each year. Stenström continues by explaining that, “Thanks to its 78 ft. (24 m) reach with a banana boom, not only do we have more reach but also a greater reach depth. As a result, we can position the material accurately and easily. Also, with the faster cycle times, we get to move more material quicker.”
Still in the decision-making phase: Test drive at a comparable application
To gain a complete understanding of the SENNEBOGEN machines, Delta Terminal was invited to do a “test drive” during their project planning phase. “At that time, we took one of our operators along because, after all, he has to feel comfortable in the machine to achieve the best results,” Johan Stenström tells about the decision-making phase. With the Mastercab, Delta Terminal finally chose a version of a large-capacity port cab, where the operator works at a viewing height of around 36 ft. (11 m). It offers a clear advantage: the improved overview of the ship’s hull means that materials can be loaded faster and with greater accuracy. For maximum precision in loading operations, an additional camera was installed on the stick, which transmits the handling situation in the hull directly to a screen inside the cab.
How to avoid damage to the vessel’s structure?
Just as importantly, SENNEBOGEN’s Safety Boom Lift System helps the operator avoid damage to the vessel’s structure. When material is picked up by the grab, the boom lifts automatically without any further action from the operator: the system proves to be especially useful when only a small amount of material remains inside the vessel and the grab could drag on the ship’s hull.
Stenström sums it up, “All in all, we opted for the SENNEBOGEN 870 E because it offered us the complete solution we had been looking for. Thanks to the Green Energy Recovery System, it consumes around a third less fuel than comparable solutions. Our operators also work more efficiently. Furthermore, the machine is engineered in such a robust way that even after three years, it is as good as new on our dock.”